Not often there is a completely new piece of equipment presented to the oil and gas industry, but in 2019 we presented the Maats Internal Bending machine (IB). It is the first pipe bending machine in the world that is able to cold bend steel pipes from the inside, a technique ideal for pipes that have an external insulation. It offers an improved flexibility and economy for any project using insulated pipes, anywhere in the world.
What are the benefits of an internal bending machine?
Not often there is a completely new piece of equipment presented to the oil and gas industry, but in 2019 we presented the Maats Internal Bending machine (IB). It is the first pipe bending machine in the world that is able to cold bend steel pipes from the inside, a technique ideal for pipes that have an external insulation. It offers an improved flexibility and economy for any project using insulated pipes, anywhere in the world.
Exploring alternative pipeline constructions
Although globally there is definitely still a future for natural gas pipelines, currently there is a strong movement in Western Europe that advocates for a drastic reduction in the use of fossil fuels, including natural gas. This shift in the industry gave us a reason to further explore other kinds of pipeline construction activities, for instance large diameter pipelines for (sea)water or pipelines used for district cooling and heating.
To a certain extent, the construction of these district heating pipelines is not that different from gas pipelines, as they both use steel pipe for transport of the medium. But there are some major differences regarding the following:
- The weld insulation of the pipes – because for district heating there are several centimeters of PU insulation and a PE casing pipe, as opposed to a 3LPE coating of a few millimeters for gas pipes.
- The bending of district heating pipe – because conventional bending (from the outside) is nearly impossible without compromising the integrity of the external insulation, factory made bends are mostly used.
Making factory bends is a time consuming and costly operation; first the bare steel pipe is bent, after which PE segments are brought around the pipe that all have to be weld together at exactly the right angle. After that, the inconsistent space between the steel pipe and the PE casing pipe is filled with PU-foam. As this is a time consuming and costly operation, Maats has been looking for a solution that simplifies the manufacturing of bends for district heating projects. The most obvious alternative to factory made bends would be to bend the pipes with a conventional bending machine. All Maats bending machines are equipped with load sensing operating hydraulics; the load sensing system assures that the force applied to the pipe is as low as possible, and therefore provides the greatest chance to prevent any damages to the jacket pipe and insulation.
Despite performing several tests, the conventional bending machines were not found suitable for bending the insulated pipes that are typically used for district heating and cooling (and for heated crude oil lines as well). As an alternative, it is possible to use pipes that have a higher density (stronger) foam, but still this is no guarantee that the force needed won’t damage the insulation, especially when the steel pipe has a wall thickness that is above normal.
Internal bending
The Maats IB is the first pipe bending machine in the world that is able to cold bend steel pipes from the inside, a technique ideal for pipes that have an external insulation, like those used for district heating and – cooling, for crude oil lines or for any other medium that has to remain within set temperature limits. It provides a high-quality alternative for factory made bends or external bending that was previously used for thermal insulated pipes. The new machine offers an improved flexibility and economy for any project using insulated pipes, anywhere in the world.
Quality and safety
When bending insulated pipe joints from the inside, the foam insulation and PE jacket pipe are left undamaged, meaning that the insulation values remain uncompromised. The internal bending process has no effect on any leak detection wires or duct for heat tracer cables being used. Because the machine works internally, it has the major advantage of having no moving parts outside the pipe during the whole bending process. Another advantage of the machine is that the pipe joint is fixed into position during the bending process, which reduces pipe handling operations with all related risks, throughout the process. As the bending process itself is largely automated, the risk of human error is minimized. This leads to a less time consuming and a cheaper operation in total.
Besides the fact that quality and safety is guaranteed, the Maats IB itself is conveniently build inside a standard 20’ container, making it easy to move to and on a jobsite. This makes the machine more flexible than any other machine that currently exists. The well thought out and compact layout makes it possible to start bending quickly after arriving on site.
Economic advantages
As stated before, the current process of making factory bends is time consuming and costly. On top of that, shipping bent pipe joints is much more expensive than the transport of straight joints. External bending, when technically viable, can only be done when using pipe joints with higher density foams, making pipes not only more expensive but also creating the need for a second pipe production line, a separate storage and separate quality controls. The Maats IB only has to have standard straight pipes supplied for all bends up to 16° and it can bend up to 12 joints per day, depending on pipe length, pipe diameter, wall thickness and steel grade.
Are you interested in the ordering or discussing the possibilities of internal bending machines (IB)? Contact us at +31 (0)547 260 000 or send a mail to info@maats.com.
Maats manufactures, sells and rents out high quality equipment for the construction of pipelines with all common diameters from 6 up to 60 inches. With branch offices in Indonesia (PT. Maats), partnerships in Algeria (Maats Afrique) and Turkey (Maats Insaat) and a close cooperation with the global network of Liebherr companies, Maats’ presence is truly global.
Other news
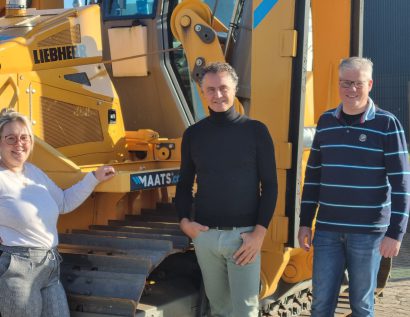
FINANCE DEPARTMENT: A CLOSER LOOK BEHIND THE NUMBERS
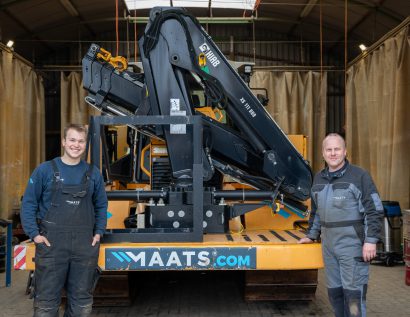
Mentoring mechanics: fostering talent and tradition at Maats Pipeline Professionals
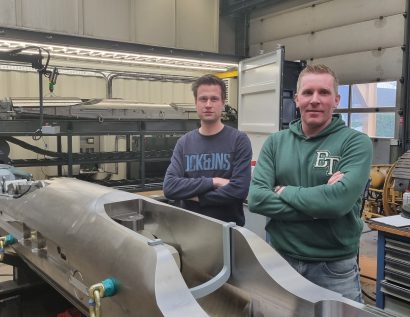
Transitioning from Hand-drawn Sketch to Advanced Machinery – Insights from the Engineering Department
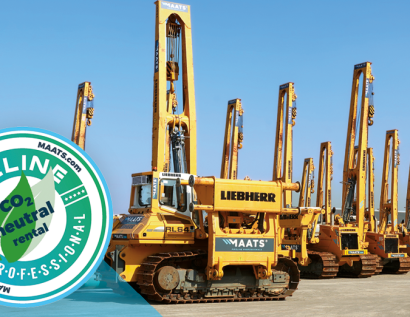
Climate neutral rental: how does it work, and what are the benefits?
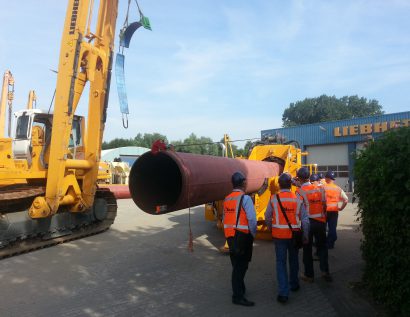
Why frequent personal contact with customers and jobsites matters
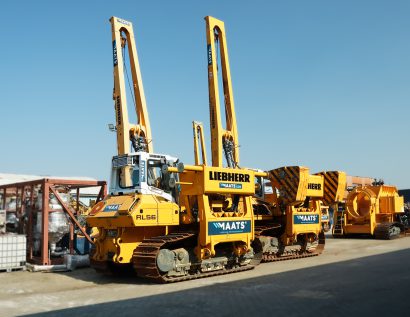
Maats and Liebherr: A Successful Collaboration
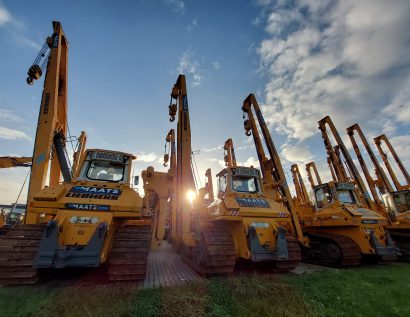
Benefits of renting pipeline equipment at Maats
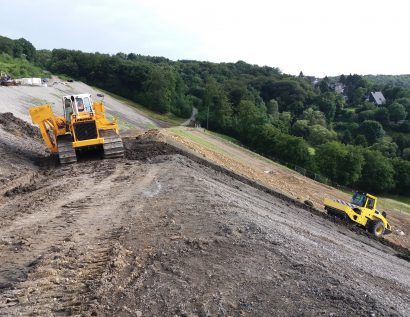
Providing a fixed rope
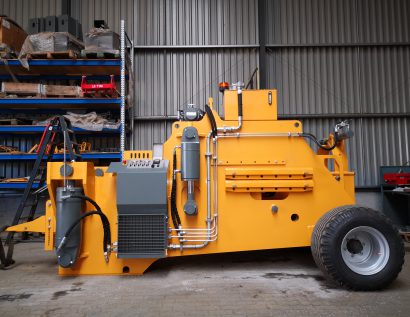
A next stage
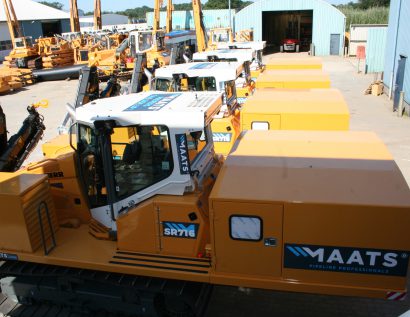